LM723 Variable Power Supply Circuit diagram
automotif wiring diagram
Saturday, January 11, 2014
Variable Power Supply Using LM723
LM723 Variable Power Supply Circuit diagram
Friday, January 10, 2014
High Current Power Supply
Since my page was first posted, I have received a number of emails asking about a high current power supply. I looked around, but couldnt find one that was suitable. So, I designed this. It is a linear supply, which might have a few of you rolling your eyes, but it takes very few parts, is simple to build and can supply huge currents
High Current Power Supply Circuit diagram :
Parts Table :
Part | Total Qty | Description |
R1 | 1 | 680 Ohm 1/4 Watt Resistor |
C1 | 1 | 20,000 - 50,000uF 20-40 Volt Capacitor |
C2, C3 | 2 | 100uF 50 Volt Capacitor |
C4 | 1 | 0.1uF 50 Volt Capacitor |
C5 | 1 | 0.01uF 50 Volt Capacitor |
D1 | 1 | Zener Diode (See Notes) |
Q1 | 1 | 2N3055 Or Other (See Notes) |
T1 | 1 | Transformer (See Notes) |
BR1 | 1 | Bridge Rectifier (See Notes) |
S1 | 1 | SPST 250 VAC 10 A Switch |
MISC | 1 | Case, Line Cord, Heatsink For Q1, Binding Posts For Output |
Notes :
- D1 should be rated at about one volt higher than then desired output of the supply. A half watt diode will do.
- Q1 can be a transistor similar to the 2N3055. I chose the 2N3055 for its availability and power handling (150 watts).
- T1 should be about 5 volts higher than the desired output of the supply, and rated for about one amp more of current. The voltage overhead is required by the regulator section. The extra current is to keep the transformer from over heating.
- The choice of BR1 will depend on the voltage and current of your transformer. The rectifier should be rated for 50 volts more than the transformer, and 5 amps more than the transformer.
- The value of R1 will be smaller when supplying high currents. Expiriment until you get what you need.
- Heatsink and fans are absolutely necessary!
Mains Pulser

Build a Room Ioniser Circuit Diagram
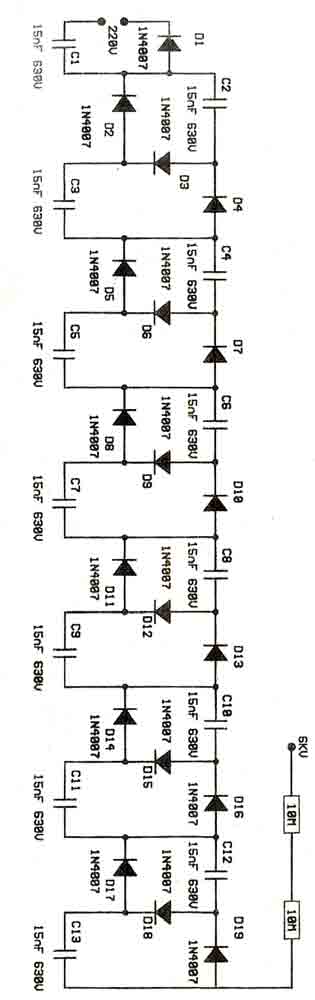
Thursday, December 26, 2013
High Voltage Generator

Tuesday, December 24, 2013
Three Phase Appliance Protector

Sunday, December 22, 2013
Motional Feed Back Amplifier
This concept has appeared long back in Practical Electronics a UK based Magazine. Based on this concept I designed this circuit during 1981 to 1986 with lots of field trials and modifications, the design was frozen in 1986. I have assembled so many amplifiers for me and for my friends based on this design with various power levels. They are still kicking in so many houses. This concept can be applied to any existing amplifier also. You must listen to believe the crystal clear thumping bass response. crystal clear mid and hi frequencies. Good transient response with very low distortion. Hope you guys will enjoy the reproduction of this amplifier.
In the art of audio sound reproduction it is well-known that the dynamic loudspeaker is more nonlinear and generates more distortion than all the other system components combined. This is particularly true at low frequencies which require large cone excursions where the stiffness of both the inner spider and the outer surround increases rapidly as the cone approaches its peak displacement, resulting in a nonlinear suspension compliance generating high distortion.
For example, in a typical high fidelity sound system at a frequency of about 35 Hz the total harmonic distortion of the amplifier might be of the order of 0.01%, whereas the distortion of the loudspeaker might range from about 3.0% to about 50.0%, depending upon the loudness. If this cone motion can be sensed and given as a feed back to the earlier stage of the amplifier, this distortion can be reduced dramatically.
Circuit diagram:
Motional Feed Back Amplifier Circuit Diagram
Motional Feedback (MFB) was a speaker system developed in the early 1970s by Philips Holland. It introduced a feedback system to the woofers of HiFi loudspeakers, enabling them to achieve a more extended low frequency response in a relatively small enclosure. The key benefits are a very controlled bass response. Any distortion induced by the enclosure or the woofer itself is immediately corrected by the feedback. These hand-built speakers were sounding very good and were quite expensive.
As a different approach, instead of using the cone movement, the current flow through the voice can be sensed (the current is proportional to cone movement) and can be used as a cone movement feedback. This novel idea is used in this amplifier design (I don’t claim any originality; this idea has appeared in Practical Electronics UK Magazine – long back – They might have even patented it).the amplifier used here is a standard Philips audio application circuit, with a specification of 40 Watt RMS @ < 0.06% Total Harmonic Distortion into 8 ohms impedance speaker and having a frequency response from 20Hz to 100 KHz, suitably modified for our application.
Powersupply Circuit:
Motional Feed Back Amplifier Powersupply Circuit Diagram
The amplifier is a conventional class B directly coupled quasi complimentary out put stage, operating with single 56Volt supply (no need for a regulated or dual power supply). BC157 is the pre-driver and half supply stabilizer. BD 139 is the driver, a BD139 and a BD140 complimentary pair out put driver stage with 2N3055 as final out put stage. The speaker voice coil current is sensed through 0.47 ohms resistance connected from speaker one end to ground. This signal is given as negative fed back to previous stage through 470 ohms. The half supply at speaker coupling capacitor can be adjusted by varying the 39K resistance (if required you may fix a 100K pre set in the place of 39K and adjust for half supply with no in put signal at junction of both 0.47 ohms of out put transistors and speaker coupling capacitor).
The quiescent current through output transistors can be adjusted with 22 ohms in series with two bias diodes 1N4007. The value for 50mA quiescent current will lie between 15 to 33 ohms for a supply of 56volts. The amplifier can be protected with a simple 1.5Amp fast acting fuse in the positive power supply. the amplifier can be assembled on 40watt Philips amplifier application board or on any standard plain straight line board. All the three driver transistors require cooling clips. (Standard TO220 casing cooling fins). Out put transistors require a good quality extruded alloy heat sink with insulating mounting kit and with a smear of silicon conductive grease, for good conductance of heat.